Com es mecanitzen les peces d'alta precisió
2023-09-22
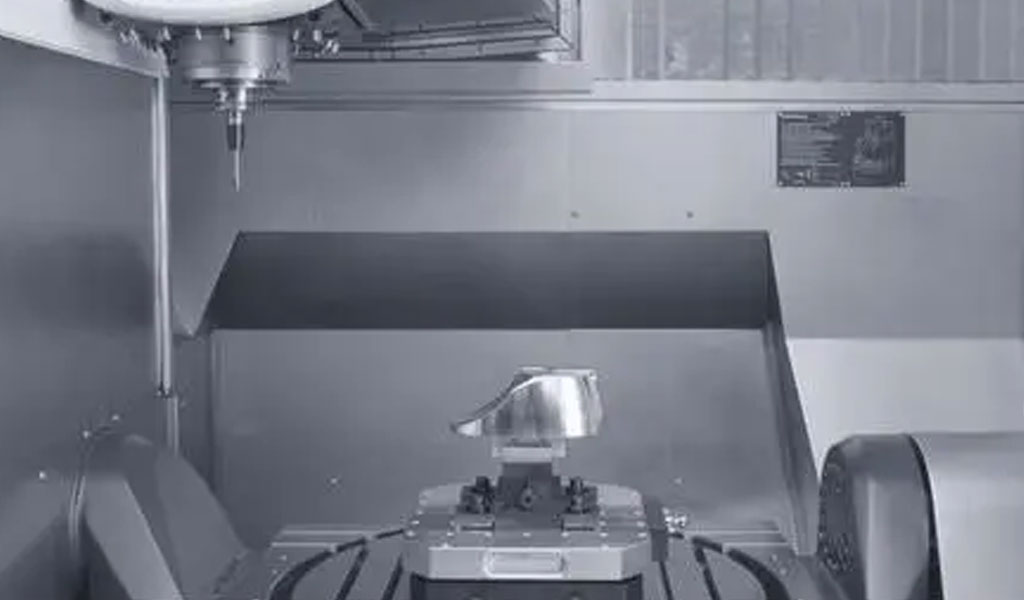
Entendre el mecanitzat de precisió
El mecanitzat de precisió és una pedra angular de la fabricació moderna, responsable de produir components complexos i precisos utilitzats en una àmplia gamma d'indústries. Per entendre-ne plenament la importància, explorem els conceptes bàsics del mecanitzat de precisió, el seu paper vital en diversos sectors i el recorregut històric que ha portat al seu estat d'excel·lència actual.A. Què és el mecanitzat de precisió?
El mecanitzat de precisió es refereix a un conjunt de processos de fabricació que eliminen material d'una peça amb un alt grau de precisió i control, donant com a resultat components finament elaborats amb toleràncies estrictes. Aquest procés transforma les matèries primeres, com ara metalls, plàstics o ceràmica, en peces precises que compleixen especificacions exigents. Les característiques clau del mecanitzat de precisió inclouen:- Precisió: El mecanitzat de precisió garanteix que el producte final s'ajusta precisament al disseny previst, amb una desviació mínima.
- Toleràncies estretes: Permet la producció de peces amb toleràncies extremadament ajustades, el que significa que els components acabats s'adhereixen estretament a les mesures especificades.
- Acabat superficial superior: El mecanitzat de precisió proporciona uns acabats superficials excepcionals, sovint eliminant la necessitat de processos d'acabat addicionals.
- Geometries complexes: Pot crear formes, contorns i característiques intricades, cosa que el fa indispensable en la fabricació de components amb dissenys complexos.
- Repetibilitat: Precisió procés de mecanitzatsón altament repetibles, garantint una qualitat constant en diverses parts.
- Versatilitat: Es pot aplicar a una àmplia gamma de materials, el que el fa apte per a diverses indústries.
B. Importància del mecanitzat de precisió
El mecanitzat de precisió té una importància immensa en diverses indústries crítiques, afectant diversos aspectes de la nostra vida quotidiana. Aquestes són algunes de les raons convincents de la seva importància:- Indústria aeroespacial: En el sector aeroespacial, el mecanitzat de precisió és indispensable per fabricar components que suporten condicions extremes. Motors d'avions, aterratge equip, i els elements estructurals es basen en peces mecanitzades amb precisió per a la seguretat i el rendiment.
- Dispositius Metges: Els dispositius mèdics com els instruments quirúrgics, les pròtesis i els dispositius implantables requereixen un mecanitzat de precisió per a la biocompatibilitat, la precisió i la seguretat del pacient.
- Sector de l'Automoció: Les peces mecanitzades amb precisió són essencials per a la indústria de l'automòbil per garantir la fiabilitat i l'eficiència dels vehicles. Components com ara peces del motor, sistemes de transmissió i mecanismes de frenada es basen en un mecanitzat precís.
- Electrònica i Semiconductors: El mecanitzat de precisió és fonamental en la producció de components microelectrònics i dispositius semiconductors, on les toleràncies minúscules són imprescindibles per a la funcionalitat.
- Sector energètic: La indústria energètica es basa en el mecanitzat de precisió per a la producció de peces crítiques utilitzades en la generació d'energia, incloses turbines, generadors i components de transmissió.
- Fabricació d'eines i matrius: El mecanitzat de precisió és crucial en la fabricació d'eines i matrius, que, al seu torn, s'utilitzen per crear innombrables altres productes.
- Electrònica de Consum: La producció de telèfons intel·ligents, ordinadors portàtils i altres productes electrònics de consum es beneficia del mecanitzat de precisió per garantir dissenys elegants i una funcionalitat òptima.
- Recerca i desenvolupament: Els investigadors i els científics depenen de components mecanitzats amb precisió per a experiments, prototips i equips de laboratori.
C. Perspectiva històrica
El viatge del mecanitzat de precisió es remunta a civilitzacions antigues, on els artesans hàbils utilitzaven eines rudimentàries per donar forma als materials. Tanmateix, la precisió aconseguida en aquells temps era limitada en comparació amb els estàndards contemporanis.- Mecanitzat de precisió primerenc: La revolució industrial dels segles XVIII i XIX va marcar un període cabdal en el desenvolupament del mecanitzat de precisió. La invenció de les màquines eina, com ara els torns i les fresadores, va revolucionar la fabricació permetent una major precisió i consistència.
- La Segona Guerra Mundial: El mecanitzat de precisió va tenir un paper fonamental a la Segona Guerra Mundial, ja que era essencial per produir equipament militar amb la precisió i uniformitat requerides. Aquesta època va ser testimoni dels avenços en les tècniques de mecanitzat i l'aparició de nous materials.
- Avenços de la postguerra: La postguerra va veure un augment de les innovacions tecnològiques, inclòs l'ús de màquines de control numèric per ordinador (CNC). Mecanitzat CNC va permetre operacions automatitzades i molt precises, inaugurant una nova era de fabricació.
- L'era digital: La integració d'ordinadors i programari en els processos de mecanitzat ha augmentat encara més el mecanitzat de precisió. Les màquines CNC modernes poden executar operacions complexes amb una precisió incomparable, cosa que les fa indispensables en el panorama de la fabricació actual.
Els materials i la seva importància
Els materials són la base del mecanitzat de precisió i la selecció del material adequat té un paper fonamental en la producció de peces d'alta precisió. En aquesta secció, aprofundirem en la importància de seleccionar els materials adequats, entendrem la importància de les propietats del material i explorarem els diferents factors que afecten la maquinabilitat.A. Selecció de materials
L'elecció dels materials en el mecanitzat de precisió és una decisió crítica que afecta directament el rendiment, la durabilitat i la funcionalitat del producte final. Els fabricants han de tenir en compte diversos factors a l'hora de seleccionar els materials:- Idoneïtat del material: El material ha de ser adequat per a l'aplicació prevista. Les diferents indústries i aplicacions tenen diferents requisits, com ara resistència a la temperatura, resistència a la corrosió i conductivitat elèctrica.
- Propietats mecàniques: Les propietats mecàniques com la resistència a la tracció, la duresa i la ductilitat són crucials. Per exemple, en aeroespacial, els materials amb alta resistència a la tracció són preferits per als components estructurals.
- Propietats tèrmiques: Algunes aplicacions requereixen materials amb una excel·lent conductivitat tèrmica o resistència a altes temperatures. Això és especialment important en indústries com la generació d'energia i l'electrònica.
- Resistència a la corrosió: En entorns on la corrosió és una preocupació, es prefereixen materials amb alta resistència a la corrosió, com l'acer inoxidable o el titani.
- Consideracions de pes: Indústries com l'automoció i l'aeroespacial sovint prioritzen materials lleugers com l'alumini o els compostos de fibra de carboni per reduir el consum de combustible i millorar el rendiment.
- Limitacions de costos: El cost és un factor important en la selecció del material. Els materials d'alt rendiment poden ser cars, de manera que els fabricants han d'aconseguir un equilibri entre el rendiment i la rendibilitat.
- Compliment de la normativa: En indústries com la sanitària, els materials han de complir estrictes normes reguladores de biocompatibilitat i seguretat.
- Disponibilitat: La disponibilitat de materials i les seves fonts també afecten la selecció. Alguns aliatges especialitzats o compostos poden tenir una disponibilitat limitada.
B. Propietats dels materials
Entendre les propietats dels materials és crucial per al mecanitzat de precisió. Aquestes són algunes de les propietats clau del material i la seva importància:- Resistència a la tracció: La resistència a la tracció mesura la capacitat d'un material per suportar una força de tracció sense trencar-se. És essencial per a components estructurals i peces sotmeses a esforços mecànics.
- Duresa: La duresa indica la resistència d'un material a la deformació i al desgast. Els materials durs són adequats per a eines de tall, mentre que els materials més suaus poden ser preferits per a determinades aplicacions, com ara els segells.
- Ductilitat: La ductilitat es refereix a la capacitat d'un material de deformar-se sense trencar-se quan està sotmès a esforços de tracció. Els materials dúctils són més fàcils de donar forma, però poden no ser adequats per a aplicacions que requereixen rigidesa.
- Conductivitat tèrmica: Els materials amb alta conductivitat tèrmica dissipen la calor de manera eficient. Aquesta propietat és vital en aplicacions on el control de la temperatura és crític.
- Conductivitat elèctrica: La conductivitat elèctrica és essencial en l'electrònica i els components elèctrics, on els materials han de facilitar el flux d'electricitat.
- Propietats magnètiques: Les propietats magnètiques són importants en indústries com l'electromagnètica i l'electrònica, on els materials poden necessitar ser ferromagnètics o no magnètics.
- Resistència química: Els materials han de resistir la corrosió química en ambients on estiguin exposats a àcids, bases o altres substàncies corrosives.
C. Factors de maquinabilitat
La maquinabilitat es refereix a la facilitat amb què un material es pot mecanitzar, tallar o donar forma. Està influenciat per diversos factors, com ara:- Duresa del material: Els materials més suaus són generalment més fàcils de mecanitzar, mentre que els materials més durs poden requerir eines i tècniques especialitzades.
- Formació de xips: La formació i evacuació d'encenalls durant el mecanitzat afecten l'eficiència i l'acabat superficial del procés.
- Desgast de l'eina: Els diferents materials poden causar diferents graus de desgast de l'eina, afectant la velocitat i el cost de mecanitzat.
- Refrigerant i lubricació: El refrigerant i la lubricació adequats són essencials per reduir la fricció, la calor i el desgast de les eines durant el mecanitzat.
- Velocitat de tall: La velocitat a la qual es mou l'eina de tall pel material afecta tant la productivitat com la qualitat de la superfície mecanitzada.
- Material de l'eina: L'elecció del material de l'eina de tall, com ara carbur o acer d'alta velocitat, depèn del material que s'està mecanitzant.
- Paràmetres de tall: L'ajust de paràmetres de tall com la velocitat d'avanç i la profunditat de tall pot optimitzar el procés de mecanitzat per a materials específics.
Màquines-eina per al mecanitzat de precisió
Les màquines eina són el cor del mecanitzat de precisió, permetent la transformació de matèries primeres en peces d'alta precisió. En aquesta secció, explorarem quatre tipus clau de màquines-eina utilitzades en el mecanitzat de precisió: centres de mecanitzat CNC, màquines de tornejat, rectificadores i EDM (mecanitzat de descàrrega elèctrica). Cadascuna d'aquestes màquines té un paper únic en la producció de components precisos.A. Centres de mecanitzat CNC
Els centres de mecanitzat CNC (Computer Numerical Control) són versàtils i àmpliament utilitzats en el mecanitzat de precisió. Són sistemes automatitzats que controlen el moviment d'eines de tall i peces de treball amb una precisió excepcional. Aquí teniu una visió general dels centres de mecanitzat CNC i la seva importància:- Versatilitat: Els centres de mecanitzat CNC poden realitzar diverses operacions de mecanitzat, com ara fresat, trepat i roscat. Aquesta versatilitat permet la producció de peces complexes amb múltiples característiques.
- Alta precisió: El control informatitzat de les màquines CNC garanteix un posicionament precís de les eines i uns resultats consistents, la qual cosa les fa ideals per a peces amb toleràncies ajustades.
- Automatització: Els centres de mecanitzat CNC poden funcionar contínuament, amb una intervenció humana mínima. Aquesta automatització augmenta l'eficiència i redueix el risc d'errors.
- Geometries complexes: Destaquen en el mecanitzat de formes i contorns complexos, cosa que els fa adequats per a indústries com l'aeroespacial, on els components complexos són habituals.
- Resultats repetibles: Les màquines CNC ofereixen una excel·lent repetibilitat, assegurant que cada peça produïda coincideix amb les especificacions exactes del disseny.
- Temps de configuració reduïts: Els centres de mecanitzat CNC es poden programar per canviar ràpidament entre diferents tasques, minimitzant els temps de configuració i augmentant l'eficiència de la producció.
B. Màquines de tornejat
Les màquines de tornejat s'utilitzen per crear peces cilíndriques fent girar una peça mentre una eina de tall elimina material de la seva superfície exterior. Són essencials per produir eixs, agulles i altres components amb simetria rotacional. Els punts clau sobre les màquines de tornejat inclouen:- Parts cilíndriques: Les màquines de tornejat s'especialitzen en la producció de components cilíndrics o tubulars, inclosos aquells amb rosques o ranures intricades.
- Alta velocitat: Funcionen a altes velocitats, el que els fa aptes per a peces que requereixen un acabat llis i precís.
- Operació d'un sol eix: La majoria de les màquines de tornejat són d'un sol eix i se centren a donar forma a la superfície externa de la peça.
- Eficient per a la producció en massa: El tornejat és altament eficient per a peces de producció en massa amb un mínim de residus de material.
- Màquines de torn: Les màquines de torn manuals i controlades per CNC són màquines de tornejat d'ús habitual, que ofereixen una gamma de capacitats.
C. Rectificadores
Les rectificadores estan dissenyades per a l'acabat superficial de precisió i la conformació de materials durs o abrasius. Són crucials per aconseguir toleràncies extremadament ajustades i acabats superficials superiors. Heus aquí per què les rectificadores són importants:- Precisió a nivell de micres: Les rectificadores poden assolir una precisió de nivell de micres, cosa que les fa essencials per a aplicacions que exigeixen el més alt nivell de precisió.
- Eliminació de material: Elimina el material per abrasió, permetent la correcció de les imperfeccions superficials i aconseguint una suavitat excepcional.
- Mòlta d'eines i talladors: A més del rectificat superficial, hi ha rectificadores especialitzades per esmolar eines de tall i produir perfils precisos.
- Varietat de mètodes de mòlta: Diferents tipus de rectificadores, incloses les rectificadores de superfície, les rectificadores cilíndriques i les rectificadores sense centre, satisfan diverses necessitats de mecanitzat.
- Materials endurits: El rectificat és especialment adequat per a materials endurits com l'acer d'eines i la ceràmica, on els mètodes de mecanitzat tradicionals poden ser ineficaços.
D. EDM (mecanitzat de descàrrega elèctrica)
EDM, o mecanitzat de descàrrega elèctrica, és un procés de mecanitzat no tradicional que utilitza descàrregues elèctriques per donar forma a materials. És ideal per crear peces intricades i delicades on les eines de tall tradicionals poden causar danys. Els aspectes clau de l'EDM inclouen:- Sense contacte físic: EDM no implica contacte físic directe entre l'eina i la peça, minimitzant el risc de desgast de l'eina i danys als materials fràgils.
- Alta precisió: Pot aconseguir una alta precisió i una qualitat d'acabat superficial, fins i tot amb materials excepcionalment durs.
- EDM per fil i electroerosió de ploma: Hi ha dos tipus principals de màquines d'electroerosió: tall de filferro EDM, que utilitza un elèctrode de filferro, i EDM de ploma, que utilitza un elèctrode amb forma.
- Formes complexes: EDM pot produir formes complexes, com matrius i motlles, amb detalls complexos i característiques fines.
- Zona afectada per la calor: Com que l'EDM no genera calor a la peça de treball, és adequat per a materials sensibles a la calor com els aliatges aeroespacials.
- Procés Lent: L'EDM és relativament lenta en comparació amb altres mètodes de mecanitzat, la qual cosa la fa més adequada per a feines de poca quantitat i alta precisió.
Eines de tall i eines
Les eines de tall estan a l'avantguarda del mecanitzat de precisió, i serveixen com a instruments que donen forma i transformen les matèries primeres en peces d'alta precisió. En aquesta secció, explorarem els diferents tipus d'eines de tall, la importància dels recobriments d'eines i els factors que afecten la vida útil i el desgast de les eines.A. Tipus d'eines de tall
El mecanitzat de precisió es basa en una àmplia gamma d'eines de tall, cadascuna dissenyada per a tasques i materials específics. L'elecció de l'eina de tall influeix enormement en l'eficiència i la precisió del procés de mecanitzat. Aquests són alguns tipus d'eines de tall habituals:- End Mills: Les freses d'extrem són eines versàtils utilitzades per a les operacions de fresat. Tenen múltiples vores de tall i poden eliminar material de la peça de diverses maneres, inclosa la cara, el contorn i la ranura.
- trepants: Els trepants estan dissenyats per crear forats a les peces de treball. Es presenten en diverses formes, com ara broques giratòries, broques centrals i broques indexables.
- Insercions de tornejat: S'utilitzen en les màquines de tornejat per donar forma a peces cilíndriques. Els inserts de tornejat estan disponibles en una varietat de formes i materials per adaptar-se a diferents aplicacions.
- Freses: Les freses tenen diferents formes, com ara freses de cara, molins de boles i talladores, i s'utilitzen a les fresadores per crear diverses característiques a la peça de treball.
- Escariadores: Els escariadors s'utilitzen per acabar i dimensionar els forats prèviament perforats a dimensions precises. Asseguren superfícies de forats llises i precises.
- Taps i matrius: Aquestes eines de tall s'utilitzen per a operacions de roscat. Les aixetes creen fils interns, mentre que les matrius creen fils externs.
- Rodes rectificadores: Les moles són eines abrasives que s'utilitzen per a la rectificació de superfícies de precisió. Estan disponibles en diferents materials abrasius i mides de gra.
- Broques: Les broques són eines especialitzades que s'utilitzen per tallar formes i perfils interns i externs, com ara claus i estries.
- Avellanadors i avellanadors: Aquestes eines s'utilitzen per crear rebaixats o xamfrans al voltant dels forats per tancaments.
- Bars avorrits: Les barres de mandrinar s'utilitzen en operacions de mandrinat per ampliar els forats existents amb precisió.
B. Recobriments d'eines
Els recobriments d'eines són capes primes de material aplicades a les eines de tall per millorar-ne el rendiment i la durabilitat. Aquests recobriments ofereixen diversos avantatges:- Fricció reduïda: Els recobriments com el nitrur de titani (TiN) i el carbonitrur de titani (TiCN) redueixen la fricció entre l'eina i la peça, donant lloc a un tall més suau i una vida útil més llarga de l'eina.
- Duresa millorada: Els recobriments augmenten la duresa de la superfície de l'eina, fent-la més resistent al desgast i allargant la vida útil de l'eina.
- Resistència a la calor millorada: Els recobriments poden suportar altes temperatures generades durant el mecanitzat, reduint el desgast de les eines relacionat amb la calor i augmentant la velocitat de tall.
- Propietats anti-acumulació: Alguns recobriments tenen propietats antiadherents, evitant l'acumulació de material a les vores de tall de l'eina.
- Augment de la lubricitat: Les eines recobertes han millorat la lubricitat, reduint la necessitat d'excés de refrigerant i millorant l'evacuació d'encenalls.
C. Vida útil i desgast de l'eina
Comprendre la vida útil i el desgast de l'eina és crucial per optimitzar els processos de mecanitzat i minimitzar els costos de producció. La vida útil de l'eina es refereix a la durada que una eina de tall roman efectiva abans que requereixi substitució o reacondicionament. Diversos factors influeixen en la vida útil i el desgast de l'eina:- Velocitat de tall: Les velocitats de tall més altes poden provocar un major desgast de l'eina a causa de les temperatures més altes generades durant el mecanitzat. La selecció adequada de velocitats de tall és essencial per equilibrar la vida útil i la productivitat de l'eina.
- Taxa d'alimentació: La velocitat a la qual l'eina de tall avança a la peça afecta el desgast de l'eina. Les altes velocitats d'avanç poden accelerar el desgast, mentre que les baixes velocitats d'avanç poden allargar la vida útil de l'eina.
- Profunditat de tall: La profunditat de tall influeix en la quantitat de material eliminat per passada. Els talls més profunds poden augmentar el desgast de l'eina, per la qual cosa és fonamental optimitzar la profunditat.
- Duresa del material: El tall de materials durs pot accelerar el desgast de l'eina. S'utilitzen eines i recobriments especialitzats per mecanitzar materials durs de manera eficaç.
- Refrigerant i lubricació: El refrigerant i la lubricació adequats ajuden a dissipar la calor i reduir la fricció, allargant la vida útil de l'eina.
- Material de l'eina: El material del qual està feta l'eina de tall afecta la seva resistència al desgast. Materials com el carbur i la ceràmica ofereixen una excel·lent resistència al desgast.
- Geometria de l'eina: La geometria de l'eina de tall, inclòs l'angle de rasclet, l'angle de relleu i el disseny del trencador d'encenalls, té un paper important en els patrons de desgast.
- Material de la peça: El tipus de material que es mecanitza afecta el desgast de l'eina. Els materials abrasius poden provocar un desgast més ràpid de les eines.
Processos de mecanitzat de precisió
Els processos de mecanitzat de precisió són els mètodes pels quals les matèries primeres es transformen en peces d'alta precisió amb toleràncies estrictes i acabats superficials excepcionals. En aquesta secció, explorarem cinc processos clau de mecanitzat de precisió: tornejat, fresat, trepat, rectificat i mecanitzat de descàrrega elèctrica (EDM). Cadascun d'aquests processos té un propòsit únic i s'utilitza en funció dels requisits específics de la peça de treball.A. Girar
El tornejat és un procés de mecanitzat utilitzat principalment per donar forma a peces cilíndriques. Implica girar una peça de treball mentre que una eina de tall d'un sol punt elimina material de la superfície exterior. Aquests són els aspectes clau del torn:- Parts cilíndriques: El tornejat és ideal per produir components cilíndrics com ara eixos, passadors i mànigues.
- Simetria rotacional: És molt adequat per a peces que requereixen simetria de rotació, ja que la peça gira en un torn mentre l'eina de tall la dóna forma.
- Operacions diverses: El tornejat pot dur a terme diverses operacions, com ara el revestiment, el tornejat (reduint el diàmetre), el tornejat cònic i el roscat.
- Tall d'un sol punt: Una única eina de tall elimina el material en un moviment continu, donant lloc a una eliminació eficient del material.
- Màquines de torn: Les màquines de torn manuals i controlades per CNC s'utilitzen habitualment per a operacions de tornejat.
B. Fresat
El fresat és un procés de mecanitzat de precisió versàtil que utilitza eines de tall multipunt per eliminar material d'una peça. És molt adequat per crear una àmplia gamma de formes i característiques. Els aspectes clau del fresat inclouen:- Versatilitat: El fresat pot produir superfícies planes, ranures, butxaques i contorns complexos. S'utilitza tant per a mecanitzats en 2D com en 3D.
- Tall multipunt: Múltiples vores de tall de l'eina interactuen amb la peça de treball simultàniament, permetent una eliminació eficient del material.
- Tipus de fresat: El fresat es pot realitzar amb diversos tipus de talladores, com ara freses d'extrem, freses frontals i molins de boles.
- Centres de mecanitzat CNC: Les fresadores controlades per CNC ofereixen un control precís sobre el moviment de l'eina i s'utilitzen àmpliament en el mecanitzat modern.
- Alta velocitat: El fresat es pot realitzar a altes velocitats, permetent una producció eficient.
C. Perforació
La perforació és un procés de mecanitzat de precisió utilitzat per crear forats a les peces de treball. És una operació fonamental en diverses indústries. Els aspectes clau de la perforació inclouen:- Creació de forats: Les màquines de perforació utilitzen eines especialitzades anomenades trepans per treure material i crear forats de diàmetres específics.
- Tipus de trepants: Hi ha diferents tipus de broques disponibles, com ara broques giratòries, broques centrals i broques indexables, cadascun dissenyat per a aplicacions específiques.
- Precisió: El posicionament i l'alineació precís són essencials en la perforació per garantir que els forats es creïn amb precisió.
- Velocitat i velocitat d'alimentació: Els paràmetres de perforació com la velocitat de rotació i la velocitat d'alimentació són crítics per aconseguir les dimensions del forat desitjades.
- Refrigerant i lubricació: El refrigerant i la lubricació adequats s'utilitzen per dissipar la calor i reduir la fricció durant la perforació.
D. Mòlta
El rectificat és un procés de mecanitzat de precisió que empra rodes abrasives per eliminar material i aconseguir toleràncies extremadament ajustades i acabats superficials. Els aspectes clau de la mòlta inclouen:- Precisió excepcional: La mòlta pot aconseguir una precisió a nivell de micres, la qual cosa la fa ideal per a aplicacions que requereixen la màxima precisió.
- Acabat de la superfície: produeix acabats superficials superiors, eliminant sovint la necessitat de processos d'acabat addicionals.
- materials: La mòlta és adequada per a materials durs i abrasius, com ara acer endurit, ceràmica i carburs.
- Varietat de mètodes de mòlta: Diferents tipus de rectificadores, com ara rectificadores de superfície, rectificadores cilíndriques i rectificadores sense centre, cobreixen diverses necessitats de mecanitzat.
- Refrigerant: El refrigerant adequat és essencial en la mòlta per evitar el sobreescalfament i mantenir la integritat de la roda.
E. Mecanitzat de descàrrega elèctrica (EDM)
EDM, o mecanitzat de descàrrega elèctrica, és un procés de mecanitzat de precisió no tradicional que utilitza descàrregues elèctriques per eliminar material. És especialment adequat per a mecanitzar formes complexes i complexes, així com materials durs i resistents a la calor. Els aspectes clau de l'EDM inclouen:- Mecanitzat sense contacte: EDM no implica contacte directe entre l'eina i la peça de treball, reduint el risc de desgast i dany de l'eina.
- Alta precisió: EDM pot aconseguir una alta precisió, per la qual cosa és adequat per a aplicacions on les toleràncies estrictes són essencials.
- Formes complexes: Sobresurt en el mecanitzat de formes complexes, matrius, motlles i components amb detalls fins.
- EDM per fil i electroerosió de ploma: Hi ha dos tipus principals de màquines d'electroerosió: electroerosió per filferro, que utilitza un elèctrode de filferro, i electroerosió de ploma, que utilitza un elèctrode amb forma.
- Procés Lent: L'EDM és relativament lenta en comparació amb altres mètodes de mecanitzat, la qual cosa la fa més adequada per a feines de poca quantitat i alta precisió.
Toleràncies i Control de Qualitat
El mecanitzat de precisió requereix una atenció meticulosa als detalls i un compromís rigorós amb el control de qualitat per garantir que les peces compleixen els estàndards especificats. En aquesta secció, explorarem tres aspectes crítics del control de qualitat en el mecanitzat de precisió: Dimensionament i tolerància geomètrica (GD&T), Control de processos estadístics (SPC) i Garantia de qualitat.A. Dimensionament i tolerància geomètrica (GD&T)
El dimensionament i la tolerància geomètrics, sovint abreujats com a GD&T, és un sistema utilitzat per definir i comunicar les variacions permeses de mida, forma, orientació i ubicació de les característiques d'una peça. GD&T és vital en el mecanitzat de precisió pels motius següents:- Comunicació precisa: GD&T ofereix un llenguatge estandarditzat perquè enginyers, dissenyadors i maquinistes comuniquin la intenció de disseny i els requisits dimensionals amb precisió.
- Aclariment de la tolerància: Ajuda a definir la variació acceptable en les dimensions crítiques, assegurant que totes les parts interessades entenguin les desviacions permeses.
- Qualitat millorada: GD&T promou la millora de la qualitat reduint l'ambigüitat en les especificacions de disseny, minimitzant el risc d'errors durant el mecanitzat.
- Eficiència del cost: Les especificacions clares de GD&T poden conduir a una reducció dels costos de fabricació, ja que és menys probable que les peces es descartin o requereixin una reelaboració a causa d'un malentès o d'una mala interpretació.
- Geometria complexa: És especialment útil per a peces amb geometries complexes, assegurant que totes les característiques es fabriquen amb les especificacions desitjades.
B. Control estadístic de processos (SPC)
El Control Estadístic de Processos (SPC) és una metodologia de control de qualitat que utilitza tècniques estadístiques per supervisar i controlar el procés de mecanitzat. SPC és essencial en el mecanitzat de precisió pels següents motius:- Monitorització de processos: SPC ajuda a controlar els processos de mecanitzat en temps real, identificant variacions o desviacions dels paràmetres desitjats.
- Detecció precoç de problemes: En supervisar contínuament el procés, SPC permet la detecció precoç de problemes que poden provocar peces fora d'especificacions, reduint els residus i el retreball.
- Presa de decisions basada en dades: SPC es basa en dades i anàlisis estadístiques per prendre decisions informades sobre els ajustos del procés, assegurant que el procés de mecanitzat es mantingui dins dels límits acceptables.
- Coherència millorada: SPC promou la consistència del procés i redueix la probabilitat de produir peces no conformes.
- Reducció de ferralla i reelaboració: En identificar i abordar ràpidament les variacions del procés, SPC minimitza la producció de peces defectuoses, reduint els costos de ferralla i reelaboració.
C. Garantia de qualitat en el mecanitzat de precisió
L'assegurament de la qualitat en el mecanitzat de precisió inclou un enfocament integral per garantir que les peces fabricades compleixen o superen els estàndards de qualitat especificats. Inclou diversos elements, entre els quals destaquen:- Documentació del procés: La documentació detallada dels processos de mecanitzat, inclosos els procediments operatius estàndard (SOP) i les instruccions de treball, garanteix que cada pas es realitza de manera coherent.
- Inspecció i mesura: Inspecció i mesurament rigoroses mitjançant instruments de precisió i tècniques de metrologia verificar que les peces compleixen les toleràncies i estàndards de qualitat especificats.
- calibratge: El calibratge periòdic dels equips de mecanitzat i dels instruments de mesura és essencial per mantenir la precisió i la traçabilitat.
- Verificació del material: La verificació de les propietats, la composició i la qualitat del material és fonamental per garantir que el material utilitzat compleix els requisits de disseny.
- Formació dels empleats: Els programes de formació i desenvolupament d'habilitats per a maquinistes i personal de control de qualitat garanteixen que siguin competents en les seves funcions i responsabilitats.
- Anàlisi de la causa arrel: Quan s'identifiquen peces no conformes, es realitza una anàlisi de la causa arrel per determinar l'origen del problema i implementar accions correctores.
- Millora Contínua: Una cultura de millora contínua fomenta la innovació i impulsa millores contínues en els processos de mecanitzat i els procediments de control de qualitat.
- Comentaris del client: Recollir i analitzar els comentaris dels clients ajuda a identificar àrees de millora i alinea els processos de mecanitzat amb les expectatives dels clients.
Conclusió
A. L'art i la ciència del mecanitzat de precisió
El mecanitzat de precisió es troba a la intersecció de l'art i la ciència, on la creativitat, l'habilitat i la innovació convergeixen per produir peces d'alta precisió que impulsen les indústries i donen forma al món modern. És alhora una forma d'art, que requereix l'artesania i l'experiència dels mecànics que transformen les matèries primeres en obres d'excel·lència en enginyeria, i una ciència que es basa en tecnologia d'avantguarda, ciència dels materials i processos avançats per aconseguir una precisió inigualable. El viatge del mecanitzat de precisió ens porta a través de la comprensió dels materials i les seves propietats, el domini de les eines i maquinària de tall i el control minuciós dels processos i toleràncies. Engloba el llenguatge de dimensionament i tolerància geomètrics, la vigilància del control estadístic del procés i el compromís amb l'assegurament de la qualitat. El mecanitzat de precisió té un paper fonamental en diverses indústries, des de l'aeroespacial i l'automoció fins a dispositius mèdics i electrònica, donant forma a tot, des de motors d'avions fins a juntes artificials i microxips. Permet la creació de components que funcionen amb una precisió i fiabilitat inigualables, sovint superant els límits del que és possible.B. Pensaments finals
Quan concloem aquesta exploració del mecanitzat de precisió, és evident que aquest camp no es tracta només de la creació de peces; es tracta de la creació de possibilitats. La recerca de la precisió impulsa la innovació, superant els límits del que es pot aconseguir. Tant si es tracta de l'artesania delicada necessària per crear els engranatges complexos d'un rellotge com de la tecnologia avançada necessària per fabricar components aeroespacials complexos, el mecanitzat de precisió és el centre de tot. El futur del mecanitzat de precisió està ple de promeses. Els avenços en la ciència dels materials, l'automatització i les tecnologies digitals continuen remodelant el paisatge. La miniaturització, la impressió en 3D i les pràctiques de fabricació sostenible són cada cop més destacades, donant lloc a nous horitzons per a la indústria. En un món on la precisió és més important que mai, el mecanitzat de precisió segueix sent un pilar indispensable de l'enginyeria moderna. És un testimoni de l'enginy humà i la nostra inflexible recerca de l'excel·lència en totes les facetes de la fabricació. A mesura que creixi la demanda de major precisió i components més complexos, el mecanitzat de precisió continuarà evolucionant, assolint els reptes del demà amb la mateixa dedicació i precisió que l'han definit durant segles.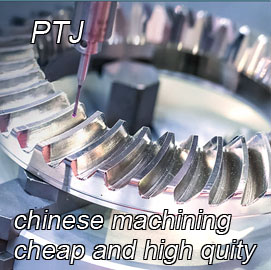
els nostres serveis
- Mecanitzat de 5 eixos
- Fresat cnc
- Torn de cnc
- Indústries de mecanitzat
- Procés de mecanitzat
- Tractament de superfícies
- Mecanitzat de metalls
- Mecanitzat de plàstics
- Motlle de metal·lúrgia de pols
- Fundició a pressió
- Galeria de peces
Estudi de Casos
- Peces de metall automàtiques
- Peces de maquinària
- Dissipador de calor LED
- Peces de construcció
- Peces mòbils
- Parts mèdiques
- Parts electròniques
- Mecanitzat a mida
- Peces per a bicicletes
Llista de materials
- Mecanitzat d'alumini
- Mecanitzat de titani
- Mecanitzat d'acer inoxidable
- Mecanitzat del coure
- Mecanitzat de llautó
- Mecanitzat de súper aliatge
- Mecanitzat Peek
- Mecanitzat UHMW
- Mecanitzat unilat
- Mecanitzat PA6
- Mecanitzat PPS
- Mecanitzat de tefló
- Mecanitzat Inconel
- Mecanitzat d'acer per a eines
- Més material
Galeria de peces